Simulation and Performance Models for Cyclic Degradation Effects in RC Bridge Columns - 4232005
Project Title—ID Number | Simulation and Performance Models for Cyclic Degradation Effects in RC Bridge Columns - 4232005 |
Start/End Dates | 10/1/05 – 9/30/06 |
Funding Source | PEER-CA State Transp. Fund |
Project Leader (boldface) and Other Team Members | Sashi Kunnath (UCD/F), Jon Mohle (UCD/GS), Zhiyu Zong (UCD/GS) |
Project goals and objectives
This project will pursue the development, validation and calibration of phenomenological material models in the context of fiber-based nonlinear beam-column elements currently implemented in OpenSees. In particular, the project will focus on the development of a reinforcing steel material model that collectively incorporate the effects of observed phenomena such as bar buckling, cyclic degradation and low-cycle fatigue. A parallel objective is the implementation of damage modeling schemes for use in performance assessment of RC structures. While this effort will focus on material-based damage models, the overall development will facilitate the incorporation of a general class of damage measures for use in performance-based seismic assessment.
Role of this project in supporting PEER's mission (vision)
The vision of this project is to contribute to a collaborative PEER effort to simulate degrading behavior of RC structures thereby enabling the prediction of post-yield damage states through collapse. The development of advanced material models will increase the reliability of fiber- based section models to better predict the inelastic response of reinforced concrete members. The implementation of damage models in OpenSees will enable the generation of damage measures conditioned on the defined demand variables. The prediction of performance (or damage) states is central to the overall PEER performance-based methodology.
Methodology employed
The proposed developments are analytical in nature and will comprise the extension and refinement of existing constitutive models. The model development will include extensive calibration/validation for the range of conditions encountered in practice (reinforcing bars in conforming and non-conforming columns, bridge piers, and wall piers), with consideration of characterizing uncertainties.
The work is expected to extend into the development and use of "damage models or indices" as both input to the bar buckling models and output for damage assessment.
Brief Description of previous year's achievements, with emphasis on accomplishments during last year (Year 8)
A new material model that incorporates the effects of bar buckling and low-cycle fatigue is developed. To facilitate the development of the model, it was first necessary to develop a base material model to describe the primary cyclic stress-strain relationships of reinforcing steel. Features of the model include the following:
Monotonic Behavior: The monotonic tensile and compressive stress-strain curves are based on a model proposed by Chang and Mander (1994) with several modifications. Only the tension backbone curve is required to be input by the user. The curve is then transformed from engineering stress-strain space to natural stress-strain space (accounting for the instantaneous change in cross-section area as the bar is stressed). This transformed curve is used to generate both the tensile and compressive backbone curves. The stress-strain conversion follows the assumption that the steel volume remains constant as detailed by Dodd and Restrepo-Posada (1995).
Diminishing Yield Plateau: It has been observed that when a reinforcing bar is subjected to plastic strain reversals within the yield plateau, strain hardening will initiate at a lower strain than that of the same bar loaded monotonically. Additionally, isotropic hardening can result from repeated strain reversals and is commonly related to cumulative plastic strain. These two aspects of the stress-strain behavior of steel bars are somewhat related and that by shortening the yield plateau as a function of accumulated plastic strain, the model will have some capability to simulate both the diminishing yield plateau and isotropic hardening. The Chang and Mander model, on which this formulation is based, models only anisotropic hardening. By adding a component of isotropic hardening, the model has additional capabilities and is able to more accurately simulate test data.
Buckling Response: Two models have been implemented: Modified Gomes-Appleton Buckling Model: Figure 1 describes the use of the buckling parameters modified from Gomes and Appleton (1997).
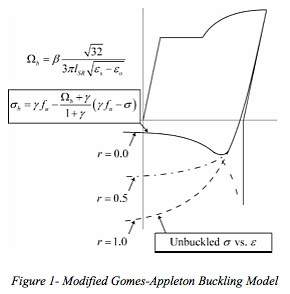
β is an amplification factor that allows the user to scale the buckling curve. The r factor adjusts the curve between the buckled curve and the unbuckled curve. The ϒ factor is the positive stress location about which the buckling factor is initiated. This factor was introduced to avoid kinks in the reloading branch. ϒ should be between 0.0 and 1.0. The variable r can only be a real number between 0.0 and 1.0. Good results have been obtained using the following values for the buckling constants: β = 1.0; r = 0.4 and ϒ = 0.5; or β = 2.0; r = 0.0 and ϒ = 0.5.
Figure 2 displays the buckling behavior due to the variation of the different constants. The response shown on the upper left is the unbuckled case. In each of the other cases, buckling behavior is defined by the constants shown.
Dhakal-Maekawa Buckling Model: This response is based on model proposed by Dhakal and Maekawa (2002). This model takes two terms, lsr and α. lsr is the slenderness ratio and α is an amplification factor. Dhakal and Maekawa suggest a value of α =1.0 for linear strain hardening and α =0.75 for elastic perfectly plastic material behavior. The material model in this implementation is neither linear strain hardening nor elastic perfectly plastic. However, since the material model does include strain hardening α=1.0 has been assumed as the default value. Figure 3 describes the basic characteristics of the model.
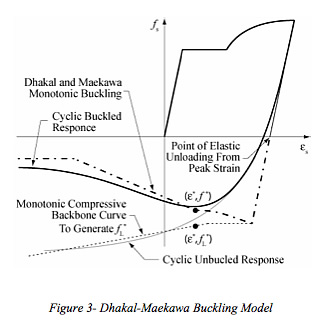
Cyclic Degradation: Cf and α are factors used to relate the number of half cycles to fracture to the half cycle plastic strain amplitude (Figure 4a). Plastic strain half cycle amplitude is defined by Equation 1. The total half cycle strain amplitude, εt, is shown in Figure 4b as the change in strain from reversal A to reversal B.
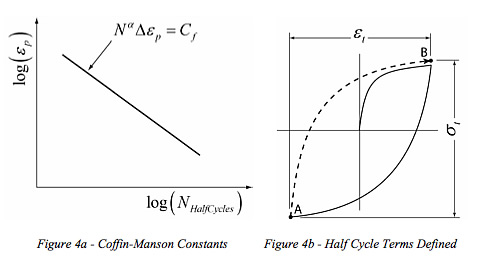
Cf and α are used to define a cumulative damage factor, D, as described in Equation 2.

The cumulative damage factor is zero at no damage and 1.0 at fracture. Once a bar has been determined to have fractured, the strength is rapidly degraded to zero.
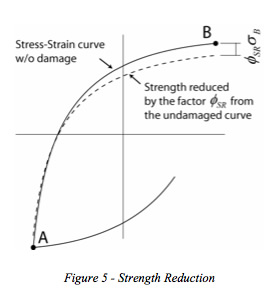
A degrade constant, K1, is used to describe loss in strength due to damage or other phenomenon resulting in softening due to plastic reversals. The degradation is currently assumed to have a simple linear relationship with D. This is used to correlate strength degradation to the cumulative damage factor. This linear relationship is shown in Equation 3

The constants K1 and Cd can be related as shown in Equation 5.

Suggested starting values have been obtained from data reported by Brown and Kunnath (2000) for bars with a slenderness of 6.0. Note that this experimental data is limited and additional calibration will be necessary to capture realistic behavior in a reinforcing bar embedded in concrete and influenced by other factors such as confinement. The initial suggested values are: α: 0.506; Cf: 0.26; Cd: 0.389
Sample Simulations of Degradation Behavior
The parameter α is best obtained from calibration of test results and is used to relate damage from one strain range to an equivalent damage at another strain range. This is usually constant for a material type. The parameter Cf is the ductility constant used to adjust the number of cycles to failure. A higher value for Cf translates to a larger number of cycles to failure. Finally, Cd is the strength reduction constant. A larger value for Cd will result in a lower reduction of strength for each cycle. The four charts shown in Figure 6 demonstrate the effect that some of the variables have on the cyclic response.
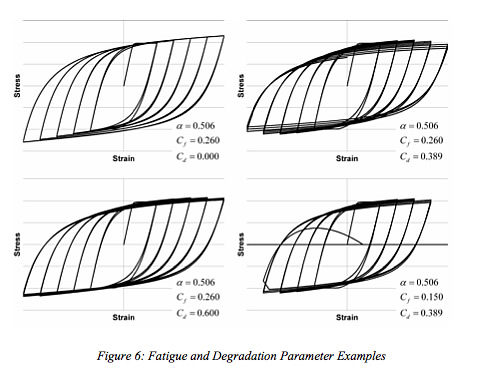
In Figure 6, the upper left response contains no strength degradation (Cd = 0.0). The upper right response shows strength degradation due to the suggested values of Cf, α, and Cd. The response shown on the lower left demonstrates the change in the response when the suggested values of Cf and α are used with Cd=0.6. An increase in the value of Cd results in less strength reduction. The response on the lower right uses the suggested values but Cf is changed to 0.15. This results in a more rapid damage accumulation causing the bar to fail sooner. Note however that the strength degradation is unaffected. The strength reduction and failure are not interdependent making the model easier to calibrate.
The above formulation has been implemented in OpenSees as a uniaxial material object. This object is intended to be used in a reinforced concrete fiber section as the steel reinforcing material. The following command is used to invoke the object and provides a significant level of control to enable the simulation of the cyclic behavior of reinforcing steel including buckling:
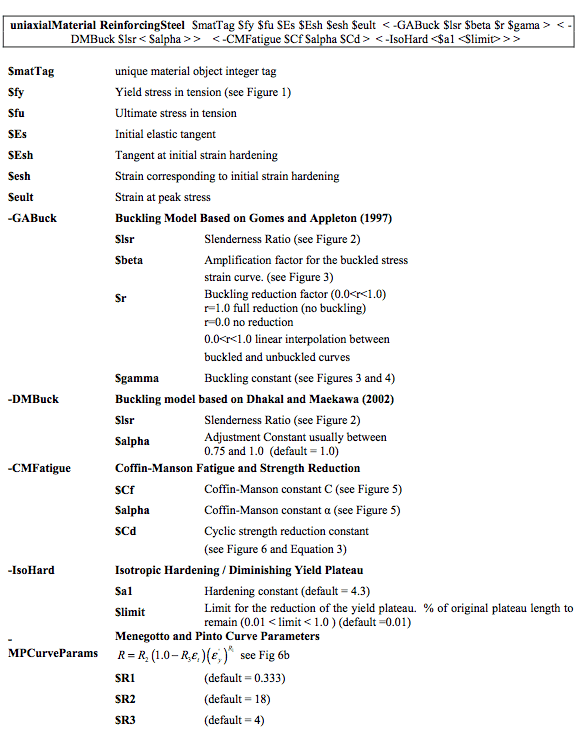
References
- Chang, G. and Mander, J. (1994). "Seismic Energy Based Fatigue Damage Analysis of Bridge Columns: Part I – Evaluation of Seismic Capacity." NCEER Technical Report 94- 0006.
- Dodd, L. and Restrepo-Posada, J. (1995). "Model for Predicting Cyclic Behavior of Reinforcing Steel" J. Struct. Eng., 121(3), 433-445.
- Gomes, A., and Appleton, J. (1997). "Nonlinear Cyclic Stress-Strain Relationship of Reinforcing Bars Including Buckling." Eng. Struct., 19(10), 822–826.
- Brown, J. and Kunnath, S.K. (2000). "Low Cycle Fatigue Behavior of Longitudinal Reinforcement in Reinforced Concrete Bridge Columns." NCEER Technical Report 00- 0007.
- Dhakal, R. and Maekawa, K. (2002). "Modeling for Postyield Buckled of Reinforcement" J. Struct. Eng., 128(9), 1139-1147.
Other similar work being conducted within and outside PEER and how this project differs
Within PEER, work is ongoing at Univ. of Washington (PI: Eberhard) to develop empirical models from experimental data to characterize damage states in reinforced concrete columns; research is also underway at Washington (PIs: Stanton and Lehman) to characterize buckling in longitudinal bars. The work being carried out in this project is analytical and being conducted at the material scale using a phenomenological approach. Experimental data will provide a basis to validate the approach and the ensuing developments will enable verification of the empirical modeling.
Outside PEER, there have been experimental studies investigating buckling of reinforcing bars (U of Texas, Austin). Also, some studies investigating empirical damage models have appeared in the literature (numerous institutions). However, none of these efforts involve the combined effects of degradation, low-cycle fatigue and buckling and none of the reported work focus on improving fiber-based modeling of RC members.
Describe any instances where you are aware that your results have been used in industry
n/a
Expected milestones & deliverables
A beta version of the material model has already been implemented in OpenSees and is available for general use.
Other milestones for the remainder of the project duration include:
- - Validation studies with experimental data (at component level as opposed to material level)
- - Development of a new buckling model (overcoming limitations of empirical models) and implementation in OpenSees. (This task may need to be extended to Year 10).
- - Technical paper documenting development
- - PEER report documenting development, calibration and validation studies
Back to Funded Project Archive main page