Earthquake Simulator Laboratory
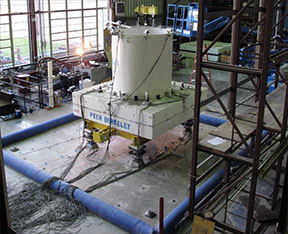
The signature piece of testing equipment at the PEER-UC Berkeley Lab is the six degree-of-freedom Shaking Table, the largest in the United States, and one of the largest in the world. The PEER-UC Berkeley Lab also houses a Large Scale Structures Lab consisting of a 20' x 60' strong floor with an integrated, reconfigurable, modular reaction wall. A comprehensive inventory of both static and dynamic hydraulic actuators, ranging from 5 kips to 2000 kips, along with an inventory of other test hardware and components are available to accommodate both simple single degree of freedom test setups as well as multi-axis custom test configurations. In addition, the PEER-UC Berkeley Lab houses large and small damper test machines, a 200 kip and a 4,000 kip uniaxial load frame, along with all of the associated control, measurement and data acquisition equipment required to operate the Lab's various test machines. The PEER facility also houses a Micro Lab for smaller scale experiments in self-equilibrating testing frames. The PEER-UC Berkeley Lab is at the forefront in the development of both hybrid control and digital image processing for the measurement of continuous strain fields.
The PEER-UC Berkeley Lab demonstrates best-practice protocol in its general Lab operation and maintains an IAS accreditation, related to the Shaking Table testing of both AC-156 and IEEE-693 test protocols. The PEER-UC Berkeley Lab has a long history of successfully providing the engineering community testing facilities, the staffing expertise to execute a given project, and the academic background to provide appropriate data analysis, design input and overall project management. The PEER-UC Berkeley Lab is available to write both academic style reports, along with AC156 and IEEE-693 reports submitted to regulatory agencies. See the "Service to Industry" web page for more information.
A welding shop, machine shop and electronics shop, along with dedicated control rooms, conference rooms and a suite of offices are also located at the PEER-UC Berkeley Lab facility.
The PEER-UC Berkeley Labs are available to both the research community and to private industry that may require large capacity testing services. Published recharge rates are utilized in the development of project budgets. Priority in scheduling a given test always favors the research community, and time is made available to commercial clients on a time-available basis
Earthquake Simulator (Shaking Table)
The Earthquake Shaking Table, dedicated in 1972, was the first modern Shaking Table and is still the largest six-degree-of-freedom (6 DOF) Shaking Table in the United States. The Shaking Table is configured to produce three translational components of motion; vertical and two horizontal, plus three rotational components; pitch, roll and yaw. These 6 DOF can be programmed to reproduce any wave form within the capacities of force, velocity, displacement and frequency of the Shaking Table system. The Shaking Table which weighs100 kips can subject structures, weighing 100,000 pounds, to horizontal accelerations of 1.5 G. Given that Shaking Table performance is a function of mass, overturning and model interaction, actual system performance is a function of these variables. Models exceeding 150,000 pounds have been successfully tested on the PEER-UC Berkeley Shaking Table. A 10-ton bridge crane services the Shaking Table Lab.
The concrete shaking table is heavily reinforced, with both traditional reinforcement and post-tensioning tendons. Structurally, the table may be considered as a one foot thick diaphragm, stiffened by central transverse ribs that extend below the table's bottom surface. The eight hydraulic actuators that drive X and Y motion, along with yaw, are attached between the Shaking Table foundation and the tables transverse ribs. The four vertical actuators, as well as the test structure, are attached to the table by post-tensioning rods, inserted through a 3' x 3' matrix of 2-5/8" conduits, penetrating the Shaking Table surface. The length of the actuator assemblies, ranging from 8'-8" in the vertical direction and 10'-6" in the horizontal direction, serve to effectively de-couple the degrees of freedom motion. The high performance capabilities of the actuators, along with corrective commands from the sophisticated, MTS 469D controller, complete the de-coupling. Read more about the Shaking Table.
Single Degree of Freedom Table
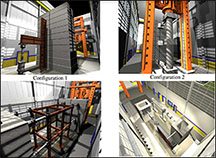
The controller is connected to a SCRAMNet ring buffer; hence, this shaking table is capable of performing real-time hybrid simulation. This platform is ideal for projects requiring large displacement such as seismically isolated structues.
Large Damper Test Machine
The Large Damper, uniaxial test machine, is designed for the testing of full-size dampers. The test machine is a self-reacting system comprised of a dynamic, servo-hydraulic actuator and a reaction frame. The actuator generates a displacement that develops a compression or tension load in the damper which is attached between the actuator and the reaction frame.
The actuator can deliver 900 kN (200 kips) at 0.38 m/sec (15 in/sec) during dynamic tests. In static loading, the actuator delivers a 1560 kN (346 kips) static force with a peak-to-peak stroke limit of (600 mm) 24 in.
Small Damper Test Machine
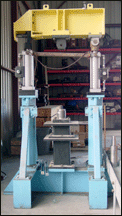
The small damper test machine is designed for the testing of small to mid size dampers, friction devices and other structural components. The test machine consists of two, dynamic servo-hydraulic actuators installed in a self equilibrating system that consists of two, dynamic servo-hydraulic actuators and a reaction frame. The actuators generate vertical displacement that develops a compression or tension load in the damper or friction device attached between the top and bottom platens of the test machine.
The system capacity is 445 kN (100 kips) at 0.50 m/sec (20 in/sec) during dynamic tests. In static loading, the actuators have a peak-to-peak stroke limit of 500 mm
(20 in).
Big Press
A Southwark-Emery, 4,000-kip Load Frame, originally built in 1932, was moved from the main campus and installed at the current PEER-UC Berkeley Lab in 1964. The uniaxial load frame can impose a 4,000 kip compression load and a 3,000 kip tension load. The maximum horizontal clearance between the vertical columns is 10'. The maximum length of a compression test element is 33.5 feet. In tension, the maximum specimen length is 22 feet. The stroke limit is 48" and the maximum rate of loading, at full capacity, is 0.071 inches per second. A dedicated hydraulic system provideshigh pressure oil to the 4,000 kip Load Frame. The load measuring emery-capsule and the associated electronic read-outs are routinely calibrated with NIST traceable equipment and procedure. A 12 ton bridge crane is accessible tothe entire Lab where the 4,000 kip Load Frame is sited. A dedicated 8 ton crane and a perimeter elevator platform, provide additional utility to the 4,000 kip Load Frame. The below the crane hook ceiling height of the Lab is 65' and the truck entry door to the Lab is 11' wide and 16' tall.
The 4,000 kip Load Frame is routinely utilized for research projects and is also available to commercial clients who require large loads to complete their required testing. An inventory of test machine specific hardware is maintained by PEER, as well as transducers, controllers and data systems.
Reaction Wall and Floor
The structural tie-down floor is located on the east end of the main bay of the laboratory. The overall plan dimensions of the tie-down slab are 20 x 60 ft. The slab has 2-1/2 inch holes located in an array of 36 inch on center over the 20 x 60 ft area. The test floor provides a completely versatile facility for testing large structural assemblies. Static or dynamic loads may be applied to specimens using tie rods, hydraulic actuators and steel loading frames. The test floor was designed to act as a hollow box girder in the longitudinal direction and as a vierendeel girder in the transverse.
Fleet of Actuators
Static | ||||
---|---|---|---|---|
Manufacturer | Model | Load Capacity kN (kip) |
Stroke mm (in) |
Quantity |
MTS | 243.70T | 1460 (328) | 1829 (72) | 3 |
Sheffer | 20HHC12 | 4180/3110 (940/700) | 300 (12) | 2 |
Sheffer | 14HHC20 | 2000/1500 (460/340) | 500 (20) | 2 |
Sheffer | 14HHC10 | 2000/1500 (460/340) | 250 (10) | 2 |
Parker | CBB 2HL 40C | 1070 (240) | 600 (24) | 1 |
Parker | CD 2H 14C | 530 (120) | 900 (36) | 2 |
Parker | BB 2H LT18A | 270 (60) | 900 (36) | 1 |
Dynamic | |||||
---|---|---|---|---|---|
Manufacturer | Model | Load Capacity kN (kip) |
Stroke mm (in) |
Quantity | Velocity, mm/sec (in/sec) |
MTS | 244.51S | 1000 (220) | 508 (20) | 2 | 508 (20) |
MTS | 244.50 | 667 (150) | 1016 (40) | 2 | 508 (20) |
Parker | 14.0.TM3Sh 24.000 |
1560/1560 (350/350) |
600 (24) | 1 | 375 (15) |
Parker | CD 2H 14C | 530 (120) | 900 (36) | 2 | 175 (7) |
Sheffer | N/A | 530 (120) | 500 (20) | 1 | 500 (20) |
Sheffer | 6HHTF/RHF20 | 380/270 (85/60) | 500 (20) | 2 | > 500 (20) |
MOOG | 85 446 | 330 (75) | 300 (12) | 1 | 750 (30) |
MTS | N/A | 310 (70) | 300 (12) | 1 | 750 (30) |
RexRoth | MT4-HH | 170 (38) | 2500 (100) | 2 | 1125 (45) |
Cunningham | Nitrogen jack, AP | 90/60 (20/13) | 250 (10) | 2 | > 1250 (50) |
Sheffer | 2.5HHTF15 | 50/50 (12/12) | 375 (15) | 2 | 625 (25) |